Kia Rio: Engine Control / Fuel System
Specifications
Items
|
Specification
|
Fuel Tank
|
Capacity
|
45 lit (11.8 U.S.gal., 47.5 U.S.qt., 39.5 lmp.qt.)
|
Fuel Filter
|
Type
|
Paper type
|
Fuel Pressure
|
RegulatedFuel Pressure
|
330 - 370kpa (3.36 - 3.77kgf/cm², 47.86 - 53.66 psi)
|
Fuel Pump
|
Type
|
Electrical, in-tank type
|
Driven by
|
Electric motor
|
Supply Voltage
|
12 V
|
Current
|
Max. 6.0 A
|
Fuel Retrun System
|
Type
|
Returnless
|
ETC Module
Throttle Position Sensor (TPS) [integrated into ETC Module]
▷ Type: Hall IC Non-contact sensor type
▷ Specification
Throttle angle(°)
|
Output Voltage (V) [Vref=5V]
|
TPS1
|
TPS2
|
0
|
0.5
|
4.5
|
10
|
0.96
|
4.05
|
20
|
1.41
|
3.59
|
30
|
1.87
|
3.14
|
40
|
2.32
|
2.68
|
50
|
2.78
|
2.23
|
60
|
3.23
|
1.77
|
70
|
3.69
|
1.32
|
80
|
4.14
|
0.86
|
90
|
4.6
|
0.41
|
98
|
4.65
|
0.35
|
C.T (0)
|
0.5
|
4.5
|
W.O.T (86)
|
4.41
|
0.59
|
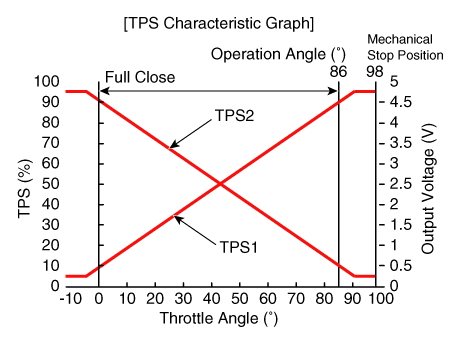
DC Motor [integrated into ETC module]
Item
|
Specification
|
Coil Resistance (Ω)
|
0.3 - 100 [20°C(68°F)]
|
Manifold Absolute Pressure
Sensor (MAPS)
▷ Type: Piezo-resistive pressure sensor type
Pressure
[kPa (kgf/cm², psi)]
|
Output Voltage (V) [Vref = 5V]
|
20.0 (0.20, 2.9)
|
0.79
|
46.7 (0.47, 6.77)
|
1.84
|
101.32 (1.03, 14.7)
|
4.0
|
Intake Air Temperature
Sensor (IATS)
▷ Type: Thermistor type
Temperature
|
Resistance (kΩ)
|
°C
|
°F
|
-40
|
-40
|
40.93 - 48.35
|
-30
|
-22
|
23.43 - 27.34
|
-20
|
-4
|
13.89 - 16.03
|
-10
|
14
|
8.5 - 9.7
|
0
|
32
|
5.38 - 6.09
|
10
|
50
|
3.48 - 3.90
|
20
|
68
|
2.31 - 2.57
|
30
|
86
|
1.9 - 2.1
|
40
|
104
|
1.08 - 1.21
|
50
|
122
|
0.76 - 0.85
|
60
|
140
|
0.54 - 0.62
|
70
|
158
|
0.40 - 0.45
|
80
|
176
|
0.29 - 0.34
|
90
|
194
|
0.22 - 0.26
|
100
|
212
|
0.17 - 0.20
|
110
|
230
|
0.13 - 0.15
|
120
|
248
|
0.10 - 0.12
|
130
|
266
|
0.08 - 0.09
|
Engine Coolant Temperature
Sensor (ECTS)
▷ Type: Thermistor type
Temperature
|
Resistance (kΩ)
|
°C
|
°F
|
-40
|
-40
|
48.14
|
-20
|
-4
|
14.13-16.83
|
0
|
32
|
5.79
|
20
|
68
|
2.31-2.59
|
40
|
104
|
1.15
|
60
|
140
|
0.59
|
80
|
176
|
0.32
|
100
|
212
|
0.19
|
110
|
230
|
0.145 - 0.149
|
120
|
248
|
0.12
|
Crankshaft Position
Sensor (CKPS)
NON- ISG Type
Item
|
Specification
|
Coil Resistance (Ω)
|
819 - 1001 [20°C (68°F)]
|
Pin
|
2
|
With ISG Type
Item
|
Specification
|
Type
|
Hall effect type
|
Air Gap (mm)
|
0.9 - 1.1
|
Pin
|
3
|
Camshaft Position Sensor
(CMPS)
Item
|
Specification
|
Type
|
Hall effect type
|
Output Pulse (V)
|
0 - 5
|
Air Gap [mm (in.)]
|
0.5 - 1.5 (0.0079 - 0.079)
|
Pin
|
3
|
Knock Sensor (KS)
Item
|
Specification
|
Resistance(MΩ)
|
4.87
|
Capacitance (pF)
|
950 - 1,350
|
Type
|
Piezo-electricity
|
Pin
|
2
|
Heated Oxygen Sensor
(HO2S)
HO2S [Bank 1/Sensor 1]
Item
|
Specification
|
Heater Resistance (Ω)
|
Approximately 9.3 [20°C(68°F)]
|
Type
|
Binary
|
Pin
|
4
|
HO2S [Bank 1/Sensor 2]
Item
|
Specification
|
Heater Resistance (Ω)
|
Approximately 9.3 [20°C(68°F)]
|
Type
|
Binary
|
Pin
|
4
|
Accelerator Position
Sensor (APS)
Accelerator
Position
|
Output Voltage (V) [Vref = 5V]
|
APS1
|
APS2
|
C.T
|
0.7 - 0.8
|
0.32 - 0.42
|
W.O.T
|
3.98 - 4.22
|
1.93 - 2.17
|
Injector
Item
|
Specification
|
Coil Resistance (Ω)
|
Approximately 9.6
|
Minimum Injection Time (ms)
|
2.5
|
Fuel Pressure
|
bar
|
2 - 7
|
kPa
|
200 - 700
|
kgf/cm²
|
2.04 - 7.14
|
psi
|
29.0 - 101.5
|
Pin
|
2
|
Purge Control Solenoid
Valve (PCSV)
Item
|
Specification
|
Coil Resistance (Ω)
|
18.5 - 22.5 [23°C (73.4°F)]
|
Pin
|
2
|
Variable Force Solenoid
(VFS)
Item
|
Specification
|
Coil Resistance (Ω)
|
6.9 - 7.9 Ω
|
Operation Voltage (V)
|
12 V
|
CVVT Oil Control Valve
(OCV)
[Bank 1 / Exhaust]
Item
|
Specification
|
Coil Resistance (Ω)
|
6.9 - 7.9 [20°C(68°F)]
|
Control Current (mA)
|
100 - 1000
|
Reted Voltage (V)
|
12
|
Insulation resistance (MΩ)
|
50 [DC 500 V/1 Min]
|
Oil Pressure
|
bar
|
2.9 - 3.1
|
kPa
|
290 - 310
|
kgf/cm²
|
2.96 - 3.16
|
psi
|
42.1 - 44.96
|
Pin
|
2
|
Ignition Timing
|
BTDC 6° ± 10°
|
Idle Speed
|
A/CON OFF
|
Neutral,N,P-range
|
660 ± 100 rpm
|
D-range
|
660 ± 100 rpm
|
A/CON ON
|
Neutral
|
660 ± 100 rpm
|
D, N, P-range
|
660 ± 100 rpm
|
Item
|
Kgf.m
|
N.m
|
lb-ft
|
ECM mounting screws
|
0.09 - 0.097
|
0.9 - 0.95
|
0.66 - 0.7
|
ECM bracket mounting bolt / nut
|
1.0 - 1.2
|
9.8 - 11.8
|
7.2 - 8.7
|
Electronic Throttle Control (ETC) moule mounting bolt
|
0.8 - 1.0
|
7.8 - 9.8
|
5.8 - 7.2
|
Engine Coolant Temperature Sensor (ECTS)
|
2.0 - 4.0
|
19.6 - 39.2
|
14.4 - 28.9
|
Crankshaft Position Sensor (CKPS) mounting bolt
|
1.0 - 1.2
|
9.8 - 11.8
|
7.2 - 8.7
|
Camshaft position sensor [Bank 1 / Intake] mounting bolt
|
1.0 - 1.2
|
9.8 - 11.8
|
7.2 - 8.7
|
Camshaft position sensor [Bank 1 / Exhaust] mounting bolt
|
1.0 - 1.2
|
9.8 - 11.8
|
7.2 - 8.7
|
Knock Sensor (KS) mounting bolt
|
1.9 - 2.4
|
18.6 - 23.5
|
13.7 - 17.4
|
Heated oxygen sensor [Bank 1 / Sensor 1]
|
4.0 - 5.0
|
39.2 - 49.1
|
28.9 - 36.2
|
Heated oxygen sensor [Bank 1 / Sensor 2]
|
4.0 - 5.0
|
39.2 - 49.1
|
28.9 - 36.2
|
Accelerator pedal position sensor (APS) mounting nut[APS integrated into
Accelerator pedal module]
|
1.3 - 1.6
|
12.7 - 15.7
|
9.4 - 11.6
|
Accelerator pedal position sensor (APS) mounting bolt[APS integrated into
Accelerator pedal module]
|
0.9 - 1.04
|
8.8 - 13.7
|
6.5 - 10.1
|
CVVT Oil Control Valve (OCV) [Bank 1 / Intake] mounting bolt
|
1.0 - 1.2
|
9.8 - 11.8
|
7.2 - 8.7
|
CVVT Oil Control Valve (OCV) [Bank 1 / Exhaust] mounting bolt
|
1.0 - 1.2
|
9.8 - 11.8
|
7.2 - 8.7
|
Item
|
Kgf.m
|
N.m
|
lb-ft
|
Fuel tank mounting nut
|
4.0 - 5.5
|
39.2 - 53.9
|
28.9 - 39.8
|
Fuel pump plate cover mounting bolt
|
0.2 - 0.3
|
2.0 - 2.9
|
1.4 - 2.2
|
Filler-neck assembly mounting bolt
|
0.8 - 1.2
|
7.8 - 11.8
|
5.8 - 8.7
|
Filler-neck assembly bracket mounting bolt
|
0.4 - 0.6
|
3.9 - 5.9
|
2.9 - 4.3
|
Delivery pipe mounting bolt
|
1.9 - 2.4
|
18.6 - 23.5
|
13.7 - 17.4
|
Delivery pipe mounting nut(↔ Fuel feed tube)
|
0.4 - 0.6
|
3.9 - 5.9
|
2.9 - 4.3
|
Special service tools
Tool Name / Number
|
Illustration
|
Description
|
Fuel Pressure Gauge
09353-24100
|

|
Measuring the fuel line pressure
|
Fuel Pressure Gauge Adapter
09353-38000
|
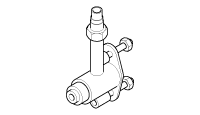
|
Connection between the delivery pipe and fuel feed line
|
Fuel Pressure Gauge Connecto
09353-24000
|
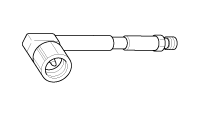
|
Connection between Fuel Pressure Gauge (09353-24100) and Fuel Pressure Gauge
Adapter (09353-38000)
|
Heated Oxygen Sensor Socket Wrench
09392-1Y100
|
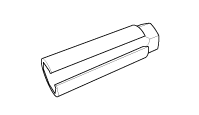
|
Removal and installation of the heated oxygen sensor
|
Troubleshooting
Basic Troubleshooting
Guide
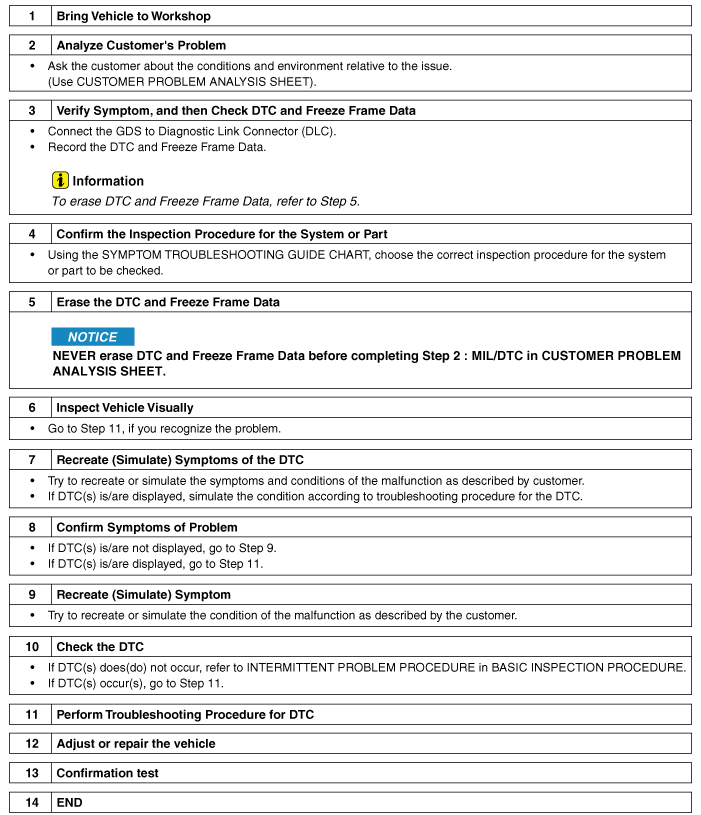
Customer Problem Analysis
Sheet
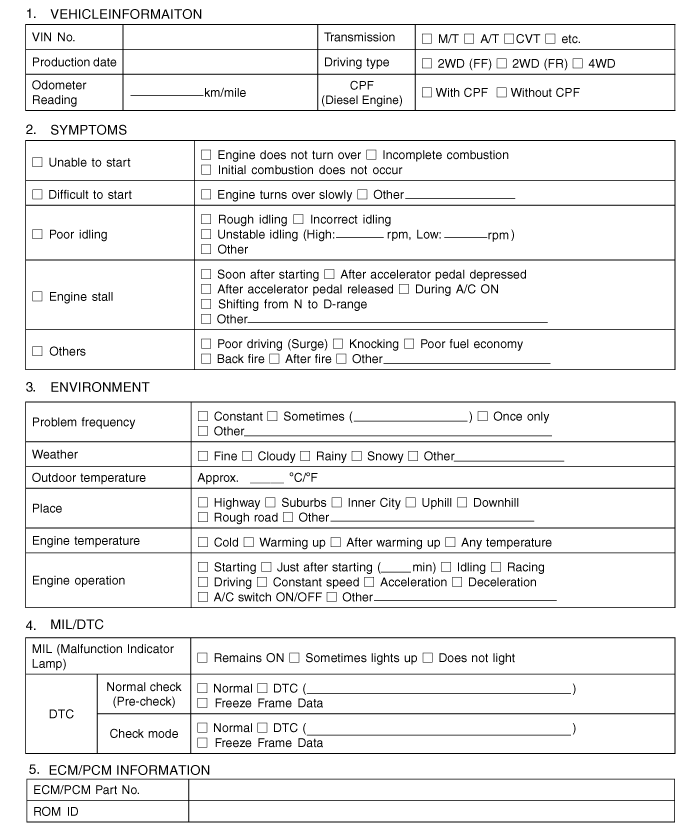
Basic Inspection Procedure
Measuring Condition
Of Electronic Parts' Resistance
The measured resistance at high temperature after vehicle running may be high
or low. So all resistance must be measured at ambient temperature (20°C, 68°F),
unless stated otherwise.
The measured resistance in except for ambient temperature (20°C, 68°F)
is reference value.
|
Intermittent Problem
Inspection Procedure
Sometimes the most difficult case in troubleshooting is when a problem symptom
occurs but does not occur again during testing. An example would be if a problem
appears only when the vehicle is cold but has not appeared when warm. In this case,
the technician should thoroughly make out a "CUSTOMER PROBLEM ANALYSIS SHEET" and
recreate (simulate) the environment and condition which occurred when the vehicle
was having the issue.
1. |
Clear Diagnostic Trouble Code (DTC).
|
2. |
Inspect connector connection, and check terminal for poor connections,
loose wires, bent, broken or corroded pins, and then verify that the connectors
are always securely fastened.
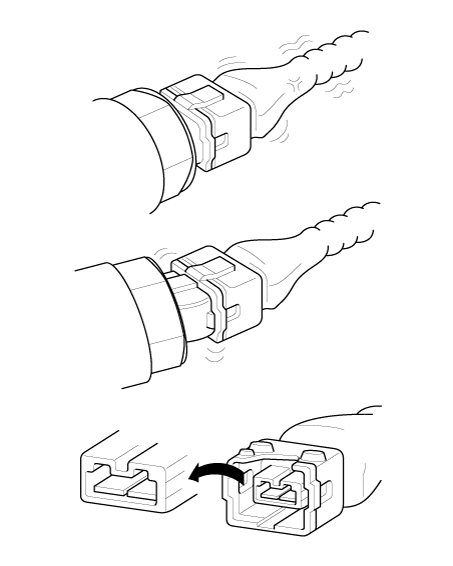
|
3. |
Slightly shake the connector and wiring harness vertically and horizontally.
|
4. |
Repair or replace the component that has a problem.
|
5. |
Verify that the problem has disappeared with the road test.
|
● SIMULATING VIBRATION
a. |
Sensors and Actuators
: Slightly vibrate sensors, actuators or relays with finger.
Strong vibration may break sensors, actuators or relays
|
|
b. |
Connectors and Harness
: Lightly shake the connector and wiring harness vertically and then
horizontally.
|
● SIMULATING HEAT
a. |
Heat components suspected of causing the malfunction with a hair dryer
or other heat source.
•
|
DO NOT heat components to the point where they may be
damaged.
|
•
|
DO NOT heat the ECM directly.
|
|
|
● SIMULATING WATER SPRINKLING
a. |
Sprinkle water onto vehicle to simulate a rainy day or a high humidity
condition.
DO NOT sprinkle water directly into the engine compartment or
electronic components.
|
|
● SIMULATING ELECTRICAL LOAD
a. |
Turn on all electrical systems to simulate excessive electrical loads
(Radios, fans, lights, rear window defogger, etc.).
|
Connector Inspection
Procedure
1. |
Handling of Connector
a. |
Never pull on the wiring harness when disconnecting connectors.
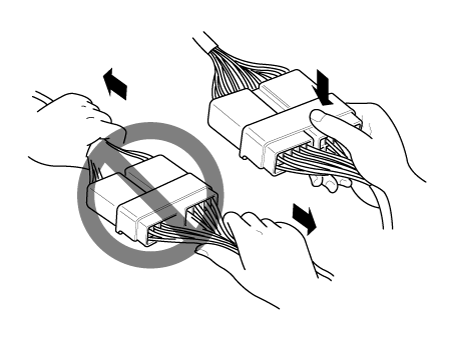
|
b. |
When removing the connector with a lock, press or pull locking
lever.
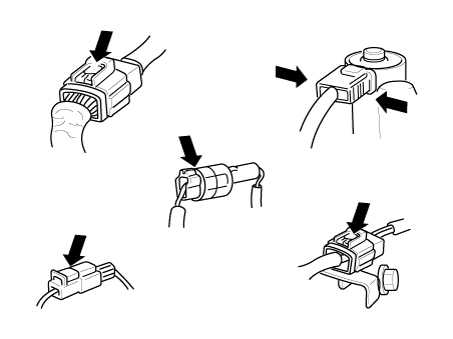
|
c. |
Listen for a click when locking connectors. This sound indicates
that they are securely locked.
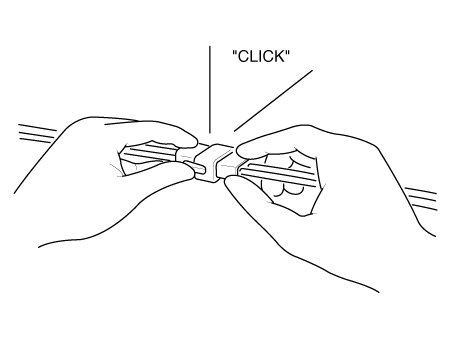
|
d. |
When a tester is used to check for continuity, or to measure
voltage, always insert tester probe from wire harness side.
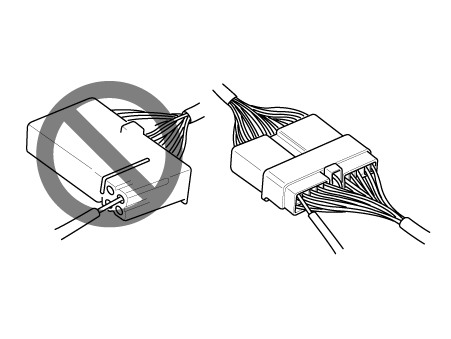
|
e. |
Check waterproof connector terminals from the connector side.
Waterproof connectors cannot be accessed from harness side.
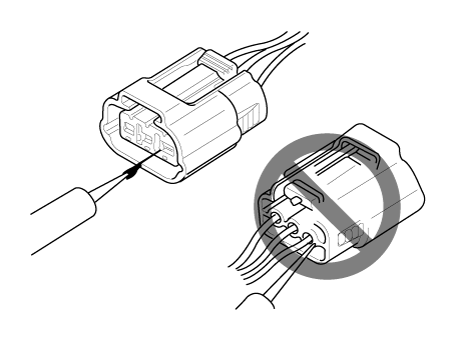
|
•
|
Use a fine wire to prevent damage to the terminal.
|
•
|
Do not damage the terminal when inserting the tester
lead.
|
|
|
2. |
Checking Point for Connector
a. |
While the connector is connected:
Hold the connector, check connecting condition and locking efficiency.
|
b. |
When the connector is disconnected:
Check missed terminal, crimped terminal or broken core wire by
slightly pulling the wire harness.
Visually check for rust, contamination, deformation and bend.
|
c. |
Check terminal tightening condition:
Insert a spare male terminal into a female terminal, and then
check terminal tightening conditions.
|
d. |
Pull lightly on individual wires to ensure that each wire is
secured in the terminal.
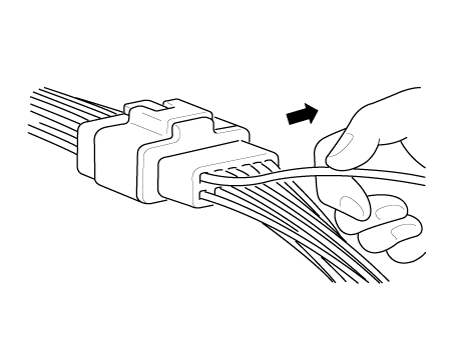
|
|
3. |
Repair Method of Connector Terminal
a. |
Clean the contact points using air gun and/or shop rag.
Never use sand paper when polishing the contact points,
otherwise the contact point may be damaged.
|
|
b. |
In case of abnormal contact pressure, replace the female terminal.
|
|
Wire Harness Inspection
Procedure
1. |
Before removing the wire harness, check the wire harness position and
crimping in order to restore it correctly.
|
2. |
Check whether the wire harness is twisted, pulled or loosened.
|
3. |
Check whether the temperature of the wire harness is abnormally high.
|
4. |
Check whether the wire harness is rotating, moving or vibrating against
the sharp edge of a part.
|
5. |
Check the connection between the wire harness and any installed part.
|
6. |
If the covering of wire harness is damaged; secure, repair or replace
the harness.
|
Electrical Circuit
Inspection Procedure
● Check Open Circuit
1. |
Procedures for Open Circuit
If an open circuit occurs (as seen in [FIG. 1]), it can be found by performing
Step 2 (Continuity Check Method) or Step 3 (Voltage Check Method) as shown
below.
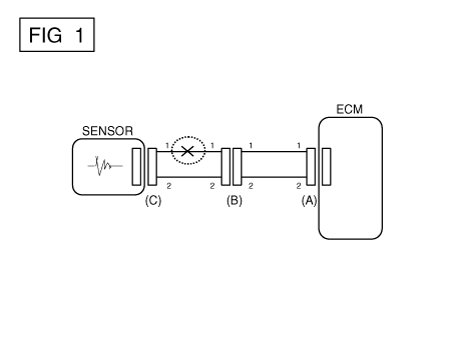
|
2. |
Continuity Check Method
When measuring for resistance, lightly shake the wire harness
above and below or from side to side.
|
Specification (Resistance)
1Ω or less → Normal Circuit
1MΩ or Higher → Open Circuit
|
a. |
Disconnect connectors (A), (C) and measure resistance between
connector (A) and (C) as shown in [FIG. 2].
In [FIG.2.] the measured resistance of line 1 and 2 is higher
than 1MΩ and below 1 Ω respectively. Specifically the open circuit
is line 1 (Line 2 is normal). To find exact break point, check sub
line of line 1 as described in next step.
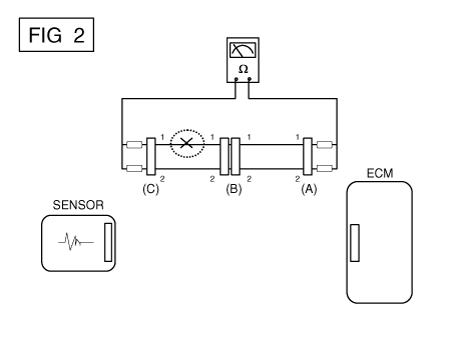
|
b. |
Disconnect connector (B), and measure for resistance between
connector (C) and (B1) and between (B2) and (A) as shown in [FIG.
3].
In this case the measured resistance between connector (C) and
(B1) is higher than 1MΩ and the open circuit is between terminal
1 of connector (C) and terminal 1 of connector (B1).
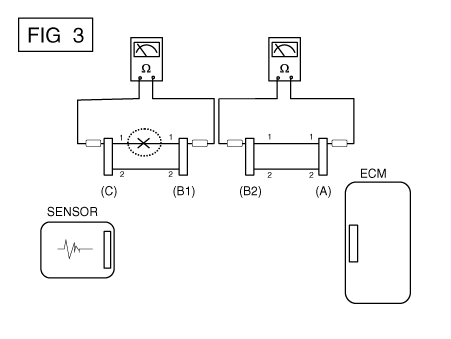
|
|
3. |
Voltage Check Method
a. |
With each connector still connected, measure the voltage between
the chassis ground and terminal 1 of each connectors (A), (B) and
(C) as shown in [FIG. 4].
The measured voltage of each connector is 5V, 5V and 0V respectively.
So the open circuit is between connector (C) and (B).
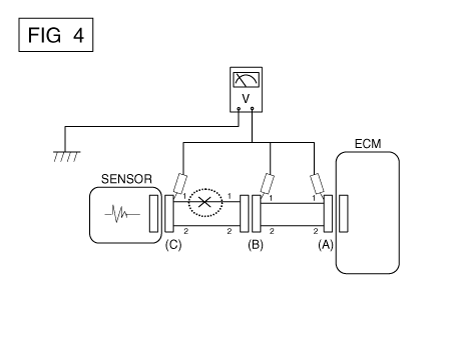
|
|
● Check Short Circuit
1. |
Test Method for Short to Ground Circuit
• |
Continuity Check with Chassis Ground
|
If short to ground circuit occurs as shown in [FIG. 5], the broken point
can be found by performing Step 2 (Continuity Check Method with Chassis
Ground) as shown below.
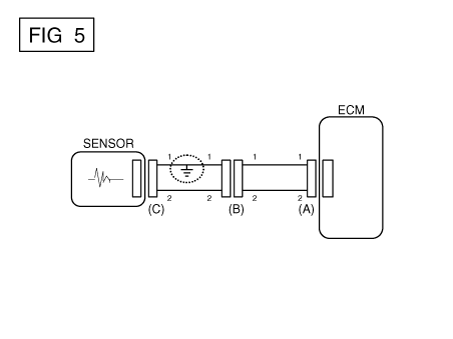
|
2. |
Continuity Check Method (with Chassis Ground)
Lightly shake the wire harness above and below, or from side
to side when measuring the resistance.
|
Specification (Resistance)
1Ω or less → Short to Ground Circuit
1MΩ or Higher → Normal Circuit
|
a. |
Disconnect connectors (A), (C) and measure for resistance between
connector (A) and Chassis Ground as shown in [FIG. 6].
The measured resistance of line 1 and 2 in this example is below
1 Ω and higher than 1MΩ respectively. Specifically the short to
ground circuit is line 1 (Line 2 is normal). To find exact broken
point, check the sub line of line 1 as described in the following
step.
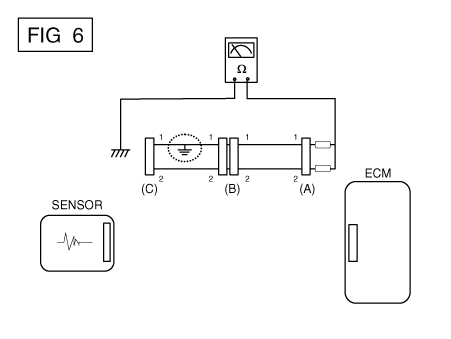
|
b. |
Disconnect connector (B), and measure the resistance between
connector (A) and chassis ground, and between (B1) and chassis ground
as shown in [FIG. 7].
The measured resistance between connector (B1) and chassis ground
is 1Ω or less. The short to ground circuit is between terminal 1
of connector (C) and terminal 1 of connector (B1).
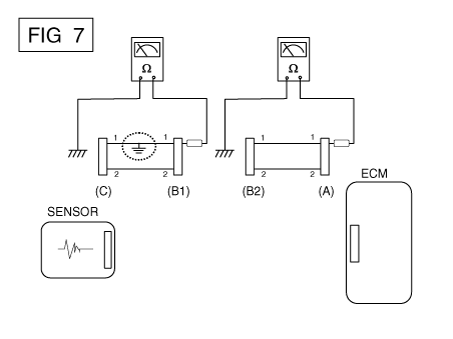
|
|
Symptom Troubleshooting
Guide Chart
Main Symptom
|
Diagnostic Procedure
|
Also Check For
|
Unable to start
(Engine does not turn over)
|
3) |
Inhibitor switch (A/T) or clutch start switch (M/T)
|
|
|
Unable to start
(Incomplete combustion)
|
2) |
Check the fuel pressure
|
3) |
Check the ignition circuit
|
4) |
Troubleshooting the immobilizer system (In case of immobilizer
lamp flashing)
|
|
• |
Slipped or broken timing belt
|
|
Difficult to start
|
2) |
Check the fuel pressure
|
3) |
Check the ECT sensor and circuit (Check DTC)
|
4) |
Check the ignition circuit
|
|
|
Poor idling
(Rough, unstable or incorrect Idle)
|
1) |
Check the fuel pressure
|
3) |
Check the long term fuel trim and short term fuel trim (Refer
to CUSTOMER DATASTREAM)
|
4) |
Check the idle speed control circuit (Check DTC)
|
5) |
Inspect and test the Throttle Body
|
6) |
Check the ECT sensor and circuit (Check DTC)
|
|
|
Engine stall
|
2) |
Check the fuel pressure
|
3) |
Check the idle speed control circuit (Check DTC)
|
4) |
Check the ignition circuit
|
5) |
Check the CKPS Circuit (Check DTC)
|
|
|
Poor driving
(Surge)
|
1) |
Check the fuel pressure
|
2) |
Inspect and test Throttle Body
|
3) |
Check the ignition circuit
|
4) |
Check the ECT Sensor and Circuit (Check DTC)
|
5) |
Test the exhaust system for a possible restriction
|
6) |
Check the long term fuel trim and short term fuel trim (Refer
to CUSTOMER DATASTREAM)
|
|
|
Knocking
|
1) |
Check the fuel pressure
|
2) |
Inspect the engine coolant
|
3) |
Inspect the radiator and the electric cooling fan
|
|
|
Poor fuel economy
|
1) |
Check customer's driving habits
|
•
|
Is A/C on full time or the defroster mode on?
|
•
|
Are tires at correct pressure?
|
•
|
Is excessively heavy load being carried?
|
•
|
Is acceleration too much, too often?
|
|
2) |
Check the fuel pressure
|
4) |
Test the exhaust system for a possible restriction
|
5) |
Check the ECT sensor and circuit
|
|
|
Hard to refuel
(Overflow during refueling)
|
1) |
Test the canister close valve
|
2) |
Inspect the fuel filler hose/pipe
|
•
|
Pinched, kinked or blocked?
|
|
3) |
Inspect the fuel tank vapor vent hose between the EVAP. canister
and air filter
|
4) |
Check the EVAP. canister
|
|
• |
Malfunctioning gas station filling nozzle (If this problem occurs
at a specific gas station during refueling)
|
|
Description and operation
Description
Continuous Variable Valve Timing (CVVT) system advances or retards the valve
timing of the intake and exhaust valve in accordance with the ECM con ...
Components and components location
Components Location
1 . ECM (Engine control module)
2 . Manifold Absolute Pressure Sensor (MAPS)
3 . Intake Air Temperature Sen ...
Other information:
Description and operation
Description
Driver Airbag (DAB) is installed in the steering wheel and electrically connected
to SRSCM via the clock spring.
It protects the driver by deploying the airbag when frontal crash occurs. The
SRSCM determines deployment of the Driver Airbag (D ...
To help achieve proper engine and powertrain performance and durability, use
only lubricants of the proper quality. The correct lubricants also help promote
engine efficiency that results in improved fuel economy. These lubricants and fluids
are recommended for use in your vehicle.
M/T : Ma ...